Different industries have different requirements for tools for digital twins. This is due to the different processes, mechanical solutions and automation components used.
Emulate3D supports a wide range of industries as standard due to its extensive libraries, functions and openness.
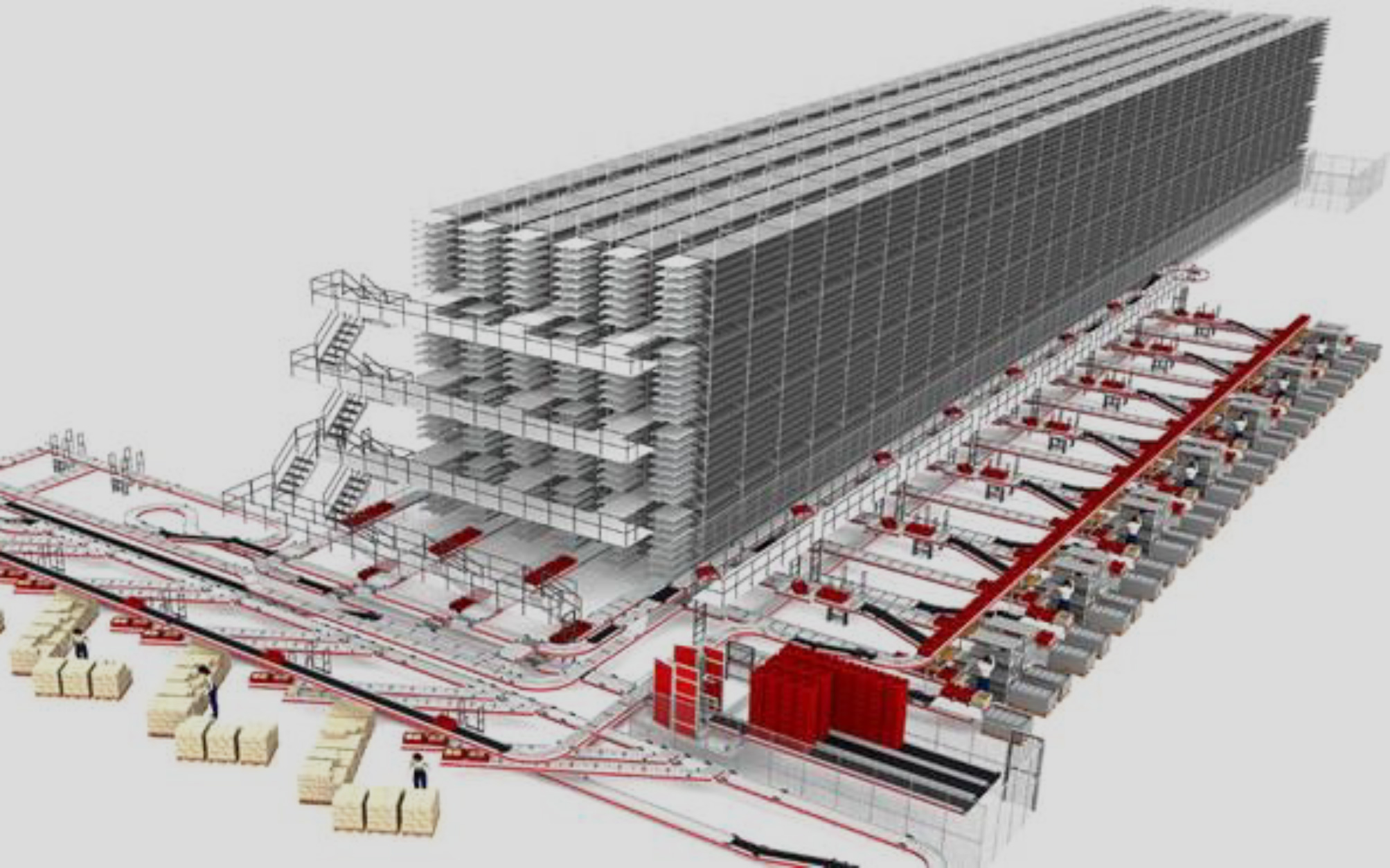
Intralogistics
Intralogistics systems are characterized by their size and generally do not require mechanical mapping down to the smallest detail. Digital twins are therefore created on the basis of extensive standard libraries. These enable the creation of very large yet powerful models, such as parcel sorting systems or baggage handling systems.
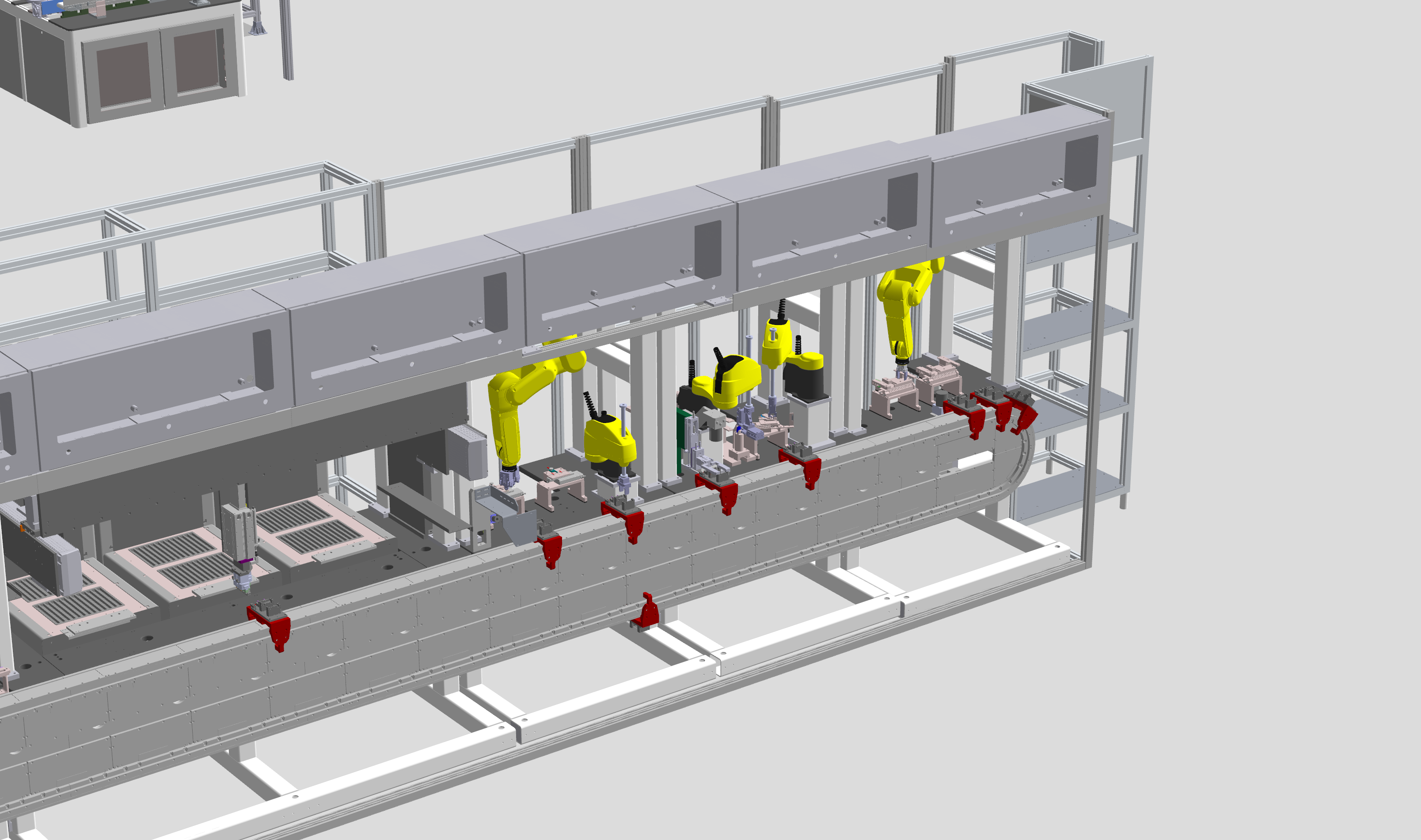
Mechanical engineering
Digital twins in mechanical engineering require very high mapping accuracy of the mechanics, including the kinematics, which is why the models are often built from the design data. Emulate3D supports this with the “CAD is the model” module, which enables the kinematization of data within Emulate3D, but also in design environments such as SolidWorks, Inventor or Creo Parametric. Robots are also frequently used in mechanical engineering, for which Emulate3D provides standard modules. However, the design can also be based on 3D CAD data. In general, missing components or functions can be added independently.
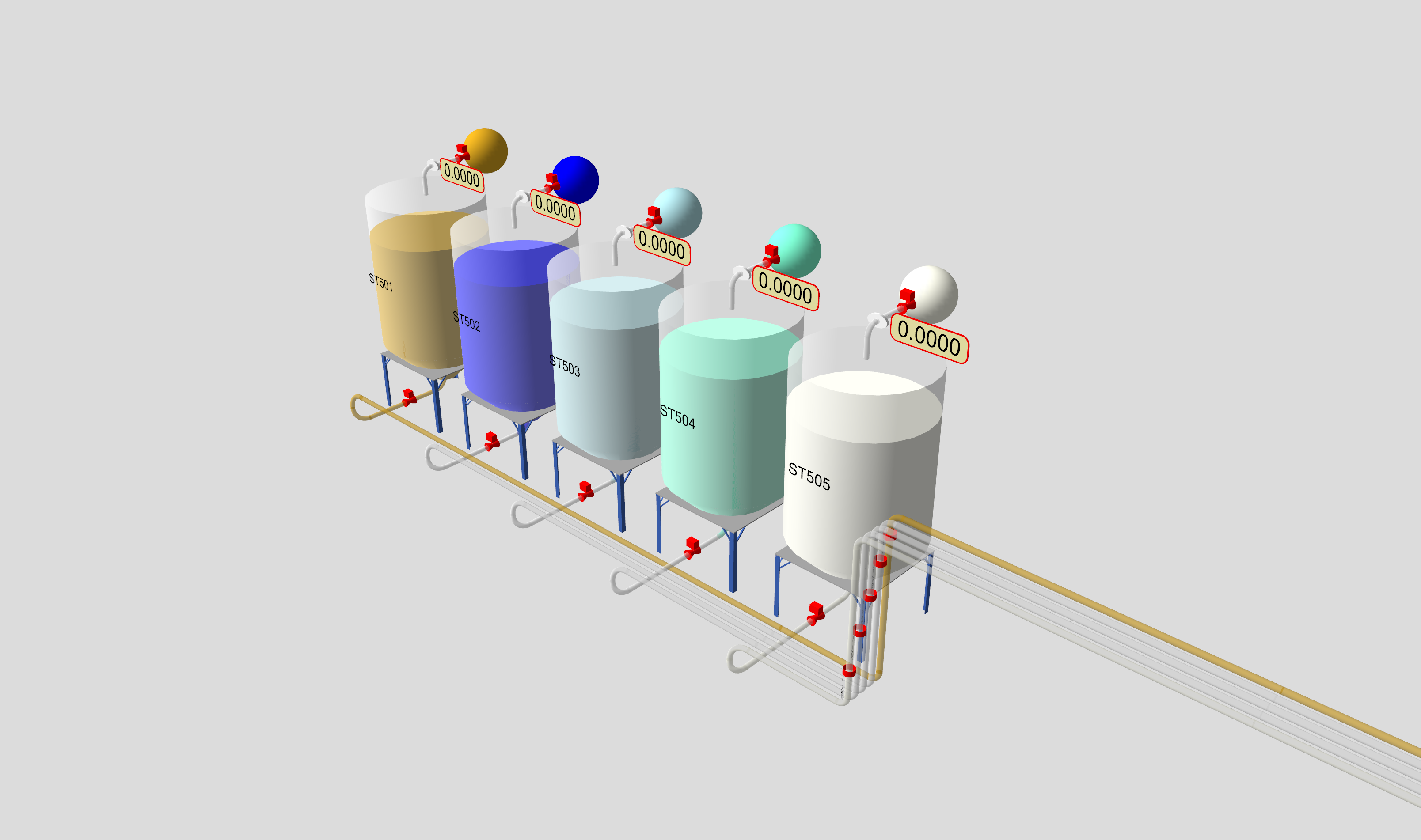
Process industry
Process plants often take on very large dimensions. Emulate3D supports the creation of digital twins in the process industry with a dedicated “Tanks and Pipes” library. This enables the semi-automated creation of models based on highly parameterizable process components such as pipe segments, tanks, valves, pumps and sensors. The flow simulation is simplified so that the modules are suitable for mixing and filling systems, for example. The automation components in the library are designed to support the PlantPAx standard, but can also be used with open automation platforms. The focus of the digital twins is on the virtual commissioning of the PLC code, both for control operation and for fault scenarios.